Концентрированные корма являются важнейшим управляющим ресурсом продукционной функции в животноводстве. Зерновые корма дают максимальный эффект в составе комбикормов, наиболее энергоемким процессом приготовления которых является измельчение. Основными недостатками широко распространенных в комбикормовой промышленности и хозяйственных условиях для измельчения зерна молотковых дробилок является высокая энергоемкость и не удовлетворительные помольные характеристики, не отвечающие требованиям ГОСТ и зоотехническим рекомендациям по содержанию пыли и остатку целых зерен на решете ш3мм рассева[1,2].
Выполненные в последние годы исследования и предложенные технические решения измельчителей позволяют существенно улучшить энерготехнологические характеристики процессов измельчения. Однако они ориентированы на уменьшение числа ударов при высоких рабочих скоростях [3,4].
Авторы выполненных исследований и схематических решений, начиная с научной школы С.В. Мельникова и последних публикаций, уделяют основное внимание «организации» процесса в устройствах различной конструкции не касаясь физики процессов деформирования[5].
Учет упруго-вязких свойств зерновок основных кормовых культур обозначил перспективу разработки процесса их измельчения в решении ступенчатого наращивания разрушающих напряжений и дефектов прочности. В результате чего наметились два пути реализации наращивания внутренних напряжений: постепенное воздействие на зерновку дисковым рабочим органом или ступенчатое (вальцами, затем молотками) (рисунок 1) [6].
Производительность вальцовой пары определяется (рисунок 1а) из геометрических и кинематических соображений по формуле [1]:

где - длина вальцов, м;
- рабочий зазор, мм принимается в зависимости от помола: мелкий – (01…0,2), средний – (0,2…0,3), крупный (0,5…0,8);
- скорость продукта в зазоре равная
, м/с;
- плотность продукта, кг/м3;
- коэффициент заполнения мелющего пространства, (0,1…0,3).
а б
а) деформация зерновки гладкими вальцами при щ1=щ2; д-рабочий зазор; б-угол защемления; dЭ-эквивалентный диаметр зерновки; RВ-радиус вальца;
б) рабочий процесс ступенчатого измельчения зерна; 1 – вальцовая секция; 2 – молотковый барабан; 3 – концентрирующие и рассеивающие деки; 4 – измельчаемый материалРисунок 1 – Схемы работы измельчителей
Мощность на привод вальцов вычисляется по формуле [2]:
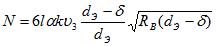
где б-угол защемления, град;
- прочностная характеристика деформируемого слоя, Па;
dЭ-эквивалентный диаметр зерновки, мм;
RВ-радиус вальцов, мм.
Анализ приведенных зависимостей даёт общее представление об энергетике процесса, однако оценка значимости и взаимодействий факторов весьма затруднительна.
Для выбора факторов модели процесса выполнена их экспертная оценка по энергоемкости и модулю помола по известной методике [8].
Для выяснений мнений экспертов была разработана анкета (таблица1), к которой прилагалась схема двухступенчатого измельчения зерна предлагаемой конструкции (рисунок 1а). В состав экспертов вошли профильные специалисты СКНИИМЭСХ и АЧИИ.
Таблица 1 – Анкета экспертной оценки факторов работы двухступенчатого измельчителя зерна
обозначение фактора | наименование фактора и единицы измерения | интервалы (уровни) варьирования | место фактора (мнение специалиста) | ||
нижний | верхний | модуль помола | энергоемкость | ||
1 | 2 | 3 | 4 | 5 | 6 |
Х1 | влажность зерна, % | 10 | 12 | ![]() |
![]() |
Х2 | подача, г/с | 200 | 600 | ![]() |
![]() |
Х3 | зазор между вальцами, мм | 1 | 3 | ![]() |
![]() |
Х4 | скорость рабочей поверхности вальцов, м/с | 5 | 11 | ![]() |
![]() |
Х5 | рабочая скорость молотков, м/с | 35 | 45 | ![]() |
![]() |
Х6 | количество пакетов молотков на барабане, шт | 2 | 6 | ![]() |
![]() |
Х7 | культура | - | + | ![]() |
![]() |
Х8 | число отражающих секций дек | 2 | 6* | ![]() |
![]() |
* – концентрирующие или рассеивающие секции дек
Результаты опроса специалистов сведены в таблицы 2 и 3 – алгоритм для определения коэффициента конкордации, в которых k – число факторов, m – число специалистов – экспертов.
В результате расчетов определены суммы и разности
по формуле [3]:
.gif)
где .
Таблица 2 – Алгоритм расчета коэффициента конкордации по модулю помола
Специалисты (m) |
Факторы (k)
|
Приме чание |
|||||||
X1 | X2 | X3 | X4 | X5 | X6 | X7 | X8 | ![]() |
|
1 | 4 | 2 | 1 | 8 | 7 | 3 | 8 | 6 | ![]() |
2 | 7 | 6 | 1 | 2 | 3 | 4 | 5 | 5 | ![]() |
3 | 3 | 6 | 1 | 4 | 2 | 5 | 7 | 8 | ![]() |
4 | 6 | 7 | 5 | 4 | 2 | 1 | 8 | 3 | ![]() |
5 | 2 | - | 1 | 3 | 5 | 6 | 4 | - | ![]() |
6 | 7 | 3 | 1 | 4 | 2 | 5 | 8 | 6 | ![]() |
7 | 7 | 6 | 4 | 2 | 1 | 3 | 8 | 5 | ![]() |
8 | 7 | 3 | 2 | 4 | 1 | 5 | 8 | 6 | ![]() |
Суммы ![]() |
43
|
33
|
16
|
31
|
23
|
32
|
56
|
39
|
L=34
|
Разности ![]() |
9
|
-1
|
-18
|
-3
|
-11
|
-2
|
22
|
5
|
![]() |
![]() |
81 | 1 | 324 | 9 | 121 | 4 | 484 | 25 |
S=1049
|
Коэффициент конкордации рассчитывался по зависимости [4] [8]:
.gif)
После вычисления коэффициента конкордации оценивали его значимость по – критерию Пирсона, равному [8]

Табличные значения критерия с числом степеней свободы
равны соответственно для уровней значимости: 0,10; 0,05; и 0,01 – 12,017, 14,067 и 18,475, что ниже полученного значения
=21,85.
Таким образом, коэффициент конкордации значительно отличается от нуля и можно утверждать, что согласованность экспертов не является случайной.
По результатам опроса и критериальной оценки их значимости строим диаграмму рангов факторов по энергоемкости (рисунок 2).
Рисунок 2 – Диаграмма рангов факторов по модулю помола
Из приведенной диаграммы рангов можно сделать вывод о том, что для дальнейших экспериментальных исследований целесообразно отобрать такие факторы как:
х3 – зазор между вальцами, мм;
х5 – рабочая скорость молотков, м/с;
х4 – скорость рабочей поверхности вальцов, м/с;
х6 – количество пакетов молотков на барабане, шт;
х2 – подача, г/с.
Аналогичным образом выполнено ранжирование факторов по энергоемкости.
Таблица 3 – Алгоритм расчета коэффициента конкордации по энергоемкости
Специалисты (m) |
Факторы (k)
|
Приме чание |
|||||||
X1 | X2 | X3 | X4 | X5 | X6 | X7 | X8 | ![]() |
|
1 | 6 | 1 | 7 | 3 | 2 | 8 | 5 | 4 | ![]() |
2 | 6 | 4 | 5 | 3 | 2 | 1 | 8 | 7 | ![]() |
3 | 6 | 5 | 3 | 4 | 1 | 2 | 7 | 8 | ![]() |
4 | 7 | 1 | 4 | 2 | 6 | 3 | 8 | 5 | ![]() |
5 | 5 | 4 | 3 | 2 | 1 | 7 | 6 | 8 | ![]() |
6 | 7 | 3 | 1 | 6 | 2 | 5 | 8 | 4 | ![]() |
7 | 7 | 4 | 3 | 2 | 1 | 5 | 8 | 6 | ![]() |
8 | 7 | 2 | 3 | 4 | 1 | 5 | 8 | 6 | ![]() |
Суммы ![]() |
51
|
24
|
29
|
26
|
16
|
36
|
58
|
48
|
L=36
|
Разности ![]() |
15
|
-12
|
-7
|
-10
|
-20
|
0
|
22
|
12
|
![]() |
![]() |
225
|
144
|
49
|
100
|
400
|
0
|
484
|
144
|
S=1546
|
Коэффициент конкордации равен:
.gif)
Оценивается значимость коэффициента конкордации по – критерию Пирсона, равному
.gif)
Табличные значения критерия также значительно ниже полученной величины
=32,21, следовательно согласованность экспертов не является случайной, что позволяет сроить диаграмму рангов факторов по модулю помола (рисунок 3).
Рисунок 3 – Диаграмма рангов факторов по энергоемкости
Из приведенной диаграммы рангов можно сделать вывод о том, что для дальнейших экспериментальных исследований целесообразно отобрать такие факторы как:
х5 – рабочая скорость молотков, м/с;
х2 – подача, г/с;
х4 – скорость рабочей поверхности вальцов, м/с;
х3 – зазор между вальцами, мм;
х6 – количество пакетов молотков на барабане, шт.
Выделенные экспертами факторы управляемые, контролируемые и независимые достаточно полно согласуются с приведенными зависимостями, что позволяет планировать многофакторный эксперимент для выяснения их влияния на критерии оптимизации (энергоемкость и модуль помола), а также оценки влияния значимости взаимодействий, что позволяет приступить к математическому планированию многофакторного эксперимента по рабочей скорости молотков, зазору между вальцами, подачи, скорости рабочей поверхности вальцов, количеству пакетов молотков на барабане.
Попадание в первую пятерку одинаковых факторов с разными рангами позволяет решить компромиссную задачу энерготехнологической оптимизации двухступенчатого процесса измельчения зерна.
Аппроксимация результатов экспериментального определения зависимости коэффициента восстановления от относительной деформации зерновок (рисунок 4) подтверждает их функциональную связь и позволяет назначить диапазон зазора между вальцами х3 в полнофакторном эксперименте для обоих критериев оптимизации.
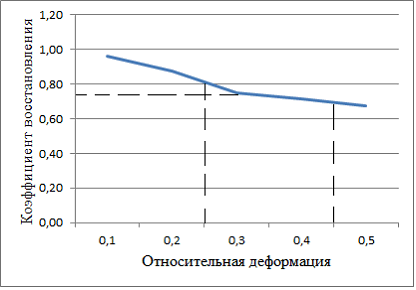
Рисунок 4 – График зависимости коэффициента восстановления от относительной деформации
Из графика (рис. 4) видно, что момент разрушения зерновки ячменя находится в пределах 0,3-0,4 высоты зерновки, при этом коэффициент восстановления равен 0,7-0,8. Коэффициент корреляции в серии опытов составил =0,98065.
Библиографический список
- Опрышко В.М. Сравнительная оценка качества продукта при измельчении в молотковой дробилке и ударно-центробежном измельчителе / В.М. Опрышко, В.В. Труфанов, С.И. Щедрин, В.В. Ляпин / Природопользование: ресурсы, техническое обеспечение: Межвузовск. сборник науч. труд. – Вып. 3. – Воронеж, 2007. – с. 267-269.
- Федоренко И.Я. Влияние числа ударов, необходимых для разрушения зерна на энергетику процесса измельчения / И.Я. Федоренко, С.В. Золотарев, А.А. Смышляев // Хранение и переработка сельхозсырья. – 2001. – №6. – с. 53–54.
- Ляпин В.В. Совершенствование рабочего процесса ударно-центробежного измельчителя / Автореф. дис…. канд. техн. наук / Воронежский государственный аграрный университет им. К.Д. Глинки. – Воронеж, - 2009. – 18с.
- Смышляев А.А. Совершенствование рабочего процесса центробежного измельчителя фуражного зерна/ Автореф. дис…. канд. техн. наук / Алтайский государственный технический университет им. Ползунова. – Барнаул, – 2002г. – 23 с.
- Долгов И.А. Математические методы в земледельческой механике / И.А. Долгов, Г.К. Васильев. – М.: Машиностроение, 1967. – 204 с.
- Шкондин В.Н. Особенности деформации зерна рабочими органами измельчителей / А.М. Семенихин, Л.А. Гуриненко, В.В. Иванов, В.Н. Шкондин // Политематический сетевой электронный научный журнал Кубанского государственного аграрного университета (Научный журнал КубГАУ) [Электронный ресурс]. – Краснодар: КубГАУ, 2014. – №03(097). – IDA [article ID]: 0971401003. – Режим доступа: http://ej.kubagro.ru/2014/03/pdf/03.pdf, 0,938 у.п.л.
- Коваленко В.П., Петренко И.М. Механизация технологических процессов в животноводстве. Краснодар, Агропромполиграфист, 2003. 432 с.
- Мельников С.В. Планирование эксперимента в исследованиях сельскохозяйственных процессов / С.В. Мельников, В.Р. Алешкин, П.М. Рощин. – 2-е изд., перераб. И доп. – Л.: Колос. Ленингр. Отд-ние, 1980. – 168 с., ил.