Концентрированные корма в кормовом балансе птицеводства составляют 93%, в свиноводстве до 90%, в скотоводстве – 30% и имеют тенденцию к увеличению в рационах высокопродуктивных животных. Стратегия машинно-технологической модернизации этих отраслей предпологает организацию на современной технической и технологической основе приготовления высококачественных комбикормов точного применения [1].
Основной и наиболее трудоёмкой операцией технологии производства комбикормов является измельчение, в соответствии с требованиями ГОСТ и зоотехническими рекомендациями, исходных компонентов – и прежде всего кормового зерна.
В настоящее время, на основе фундаментальных положений земледельческой механики, разработаны теоретические модели построения, технологической и энергетической оценки измельчителей зерна, направленные на снижения энергоёмкости процессов с учётом физико-механических свойств зерновок.
В рабочей формуле профессора С.В. Мельникова для удельной энергии измельчения, полученной на основе обобщенного закона измельчения академика П.А. Ребиндера [1, с 92-100]

Cs и Cv – коэффициенты, учитывающие, энергию на образование новых поверхностей и деформацию измельчаемых объектов;
λ – степень измельчения
Степень совершенства и эффективность процесса оцениваются его организацией с помощью коэффициента Спр, учитывающего влияние случайных факторов, способов измельчения и особенности конструкции рабочих органов.
Из приведённой зависимости (1) следует, что совершенствование процесса измельчения зерна, снижение энергоёмкости находится в области учёта свойств продукта (Cs и Cv), конструкции рабочих органов и его организации (Спр) при требуемой степени измельчения λ.
Приложение этих положений и теории измельчения к конкретной геометрии и кинематике рабочих органов измельчителей, с учётом механико-технологических особенностей и характеристик продукта, требует отдельного рассмотрения.
Рабочие органы ступенчатого измельчителя представляют собой пару дисков (рисунок 1), один из которых (верхний) неподвижный, а нижний вращается на вертикальном валу; [2].
На рабочей поверхности нижнего диска (рисунок 1) имеются подающие бороздки А, площадки релаксации В и модульный пояс С, обеспечивающие циклическое воздействие на зерновку от вхождения в рабочее пространство до полного измельчения и выходa из него.
R, Rм, R0 – радиусы, соответственно, диска, модульного пояса и приёмного окна; А – подающая бороздка; В – площадка релаксации классификатора (подающий пояс); С – модульный пояс, hвк–высота конуса верхнего диска; hнк–высота нижнего конуса;
Рисунок 1 –– Элементы рабочей поверхности дисковой пары нижнего подвижного и верхнего неподвижного
Апприори, согласно теории измельчения, размеры горизонтальных проекций участков диска регламентируются степенью измельчения и для равных переходов продуктов находятся в соотношении 1::
и так далее, если таких переходов более двух [1, с. 92-94].
Тогда площади бороздок и классификаторов подающего пояса, определяются по зависимостям
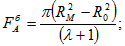
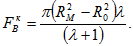
Площадь Fc поверхности модульного пояса – составит
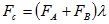
Тогда наружный радиус диска, соответствующий размерам подающего пояса, определится из равенства (3) в развернутом виде с учётом (2)

для произвольного значения – переходов между элементами и поясами измельчения.
С учётом скорости ω относительной деформации зерновок и их частей в подающих бороздках (рисунок 2) от R0 до Rм и от «а» до «в» равной

где ω0 – угловая скорость диска,·с-1;
Ri – расстояние от оси вращения диска до произвольной точки на наклонной плоскости подающей бороздки, м;
hп – суммарная высота приёмных конусов дисков, м;
α – угол подъёма дна бороздки в оксиальном сечении, град;
δм – модульный зазор между дисками, м.
Угловая скорость нижнего диска ω0 определяется из условия движения зерновок и продуктов измельчения по наклонной поверхности подающих бороздок (рисунок 2)
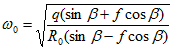
где β – угол подъема дна бороздки в радиальном направлении, град; f – коэффициент трения продуктов измельчения о дно бороздки; R0 – радиус приемного колодца, м.
А – бороздка подоющая; В – классификатор; α – угол подъёма дна бороздки в оксиальном сечении, β – то же в радиальном сечении; σп – эпюры напряжений на границах подающих элементов поверхности.
Напряжения сжатия в частицах потока, с учётом упруго-вязких свойств зерновок; составят [3]
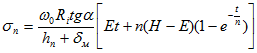
Здесь: H, E – мгровенный и длительный модули упругости соответственно, Па; t – время нахождения частицы в бороздке, с; n – время релаксации напряжений, с.
В модульном междисковом пространстве С (рисунок 1) напряжения сжатия, по аналогии с (6), определяются по формуле

где ε0 – начальная относительная деформация, полученная частицами в подающем поясе, равная

где hо – начальная высота зерновок, мм.
С учётом характера напряжений на границах бороздок и классификаторов (рисунок 2) , их размеров и коэффициентов заполнения, усилия Р дефформации сжатия потока частиц определятся зависимостями:
для бороздок
.gif)
для классификаторов
.gif)
где ψδ и ψк – соответственно коэффициенты заполнения подающих бороздок и площадок релаксации.
По аналогии с (11), с учётом (5) и коэффициента заполнения ψм модульного пространства, усилие сжатия потока в модульном поясе определится по зависимости

Мощность на процесс деформации и классификации продуктов измельчения в рабочем пространстве дисковой пары, без учёта транспортной и вентиляционной составляющих, определится по зависимости

где f – коэффициент трения продуктов измельчения о рабочие поверхности дисков.
Вращающийся нижний диск обеспечивает циклические нагружения зерновок в бороздках, удержание деформации классификаторами, свободное, под действием центробежной силы, перемещение мелких частиц к периферии подающего пояса, не препятствует движению в аксиальном направлении защемлённых частиц больших размеров. Эти частицы, достигая края подающей бороздки, попадают в свободное пространство, защемляются, разрушаются, а продукт разрушения снова выносится в классификатор и так далее.
Конструкция дозатора-распределителя [2] позволяет определить скорость зерновок на входе в приемный пояс по зависимости

в которой Rц – наружный радиус цилиндра дозатора, м; dэ – эквивалентный диаметр зерновки, м.
Тогда подача измельчителя составит
.gif)
где – ψ – коэффициент заполнения кольцевого сечения (рисунок 1) приемного пояса, по результатам эксперимента равный (0,35-0,37); ρ – плотность зерновки кг/м3.
По результатам экспериментального определения удельных энергетических и технологических характеристик рабочей модели дискового измельчителя (таблица 1): удельной производительности кг/м2·ч и удельной энергоемкости кВт·ч/т, определены параметры измельчителей модельного ряда (таблица 2)
Помол
|
Модуль
помола |
Удельная
производительность, т/м2·ч |
Удельная
энергоемкость кВт·ч/т |
Мелкий Средний Крупный |
0,76
1,69 2,28 |
4.921
11,467 18,003 |
2,99
1,89 1,14 |
№
п/п |
Fр, м2
|
Радиусы поясов
|
Площади элементов поверхности, дм2
|
Подача, т/ч
|
Мощность кВт
|
|||||||
Rn
|
Rм
|
Rн
|
Fм
|
Fn
|
Fб
|
Fк
|
0,2-1,0
|
1,0-1,8
|
1,8-2,6
|
|||
1
|
2
|
3
|
4
|
5
|
6
|
7
|
8
|
9
|
10
|
11
|
12
|
13
|
1
|
0,1
|
0,06
|
0,119
|
0,188
|
6,65
|
3,32
|
1,11
|
2,21
|
0,492
|
1,146
|
1,800
|
1,471
|
2
|
0,2
|
0,065
|
0,158
|
0,260
|
13,34
|
6,65
|
2,22
|
4,43
|
0,984
|
2,292
|
3,600
|
2,942
|
3
|
0,3
|
0,070
|
0,191
|
0,317
|
20,00
|
9,98
|
3,33
|
6,65
|
1,476
|
3,438
|
5,400
|
4,413
|
4
|
0,4
|
0,075
|
0,219
|
0,364
|
26,69
|
13,31
|
4,44
|
8,87
|
1,968
|
4,584
|
7,200
|
5,884
|
5
|
0,5
|
0,080
|
0,243
|
0,406
|
33,34
|
16,64
|
5,55
|
10,09
|
2,460
|
5,730
|
9,000
|
7,355
|
6
|
0,6
|
0,110
|
0,343
|
0,574
|
66,66
|
33,31
|
11,10
|
22,21
|
4,900
|
11,460
|
18,000
|
53,820
|
1 – мелкий помол; 2 – средний помол; 3 – крупный помол.
Содержание модульных фракций в продуктах помола, по результатам ситового анализа, составило:
Мсредний(1,69)=86,05%
Мкрупный(2,58)=97,89%
Содержание фракции менее 1 мм на поддоне рассева не превышало (3-1,9-1,2) % соответственно
Библиографический список
- Мельников С.В. Механизация и автоматизация животноводческих ферм. – Л. Колос. Ленинград отделение. 1978.–560 с.
- Пат. 2511291 Российская Федерация, МПК В02С 9/00. Дисковый измельчитель кормового зерна / Иванов В.В.; заявитель и патентообладатель ФГБОУ ВПО АЧГАА. – № 2012142839/13; заявл. 08.10.2012; опубл. 10.04.2014, Бюл. № 10.
- Ржаницын А.Р. Некоторые вопросы механики систем, деформирующихся во времени / А.Р. Ржаницын. – М. – Л.: Гостехиздат, 1949. – 252 с.
- Семенихин А.М. Физико-механические предпосылки снижения энергокмкости процесса измельчения зерна. / А.М. Семенихин, В.В. Иванов, Л.А. Гуриненко. – Ставрополь: СтавГАУ, 2010